随着汽车工业、高端家电等行业对钢铁产品的质量要求日趋严格,产品的个性化需求也越来越多。为了满足用户对产品的不同需求,真正“以客户为关注焦点”实现产品质量的稳定提升和产品质量的持续改进,通过构建“全流程质量管控系统”,将钢铁产品分散在各制造单元不同系统中的质量信息统一集中到一体化质量管控系统中,实现炼钢(熔铸)、热轧、冷轧、精整产品上下游工序间质量信息的贯通。建立以产品质量为重点,整合数据驱动方法,实现产品质量和过程参数的高效监控、评级、分析和预测。
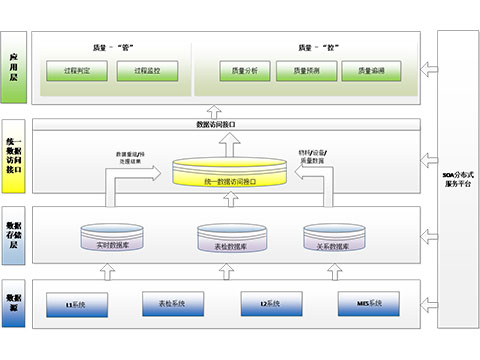
全流程质量管控系统主要包括以下功能:
1)多元异构数据采集。以现代质量管理方法为基础,依托构建的工业大数据平台,对各生产线实施多元异构数据的实时采集,采集内容包括基础自动化L1、过程自动化L2、L3、ERP、表检仪以及大型仪表的相关数据,并对采集数据以物料为对象,进行精确归集。
2)质量判定与评级。以质量设计目标为依据,开发多类判定准则引擎,对各个工序的重要产品质量(包含直接测量和软测量)指标进行精准判定,实现质量判定过程的及时性、无人化及一致性。
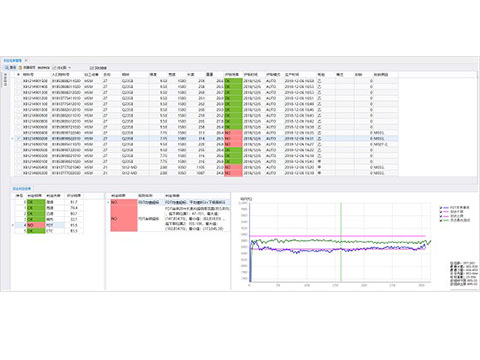
3)建立全流程过程监控系统。通过远程监控、SPC监控、规则监控等多类监控方法,对全流程各个工艺段的生产过程工艺数据进行在线监控与预警,并实现基于工艺过程的组合判定。
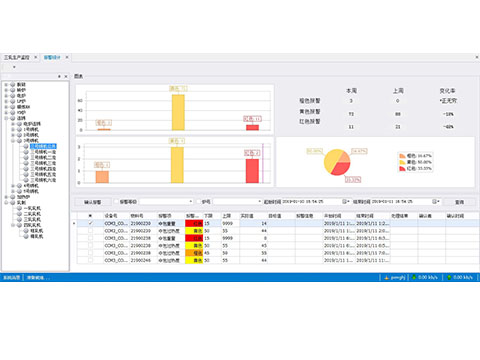
4)质量分析。针对质量异常以及质量精度的相关因素(设备,工艺,控制,操作)分析,开发基于机器学习算法的应用软件和分析工具,进行工艺和质量分析,并基于分析结果的影响因素调整工艺参数或对控制模型参数进行优化。
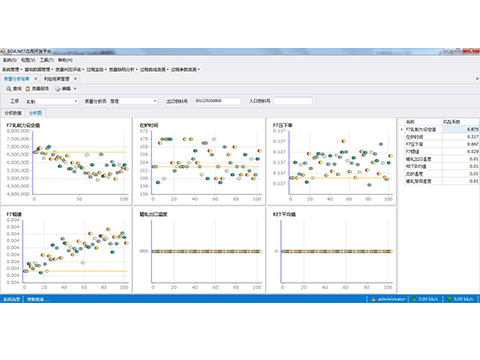
5)质量追溯。根据各工序搜集到的全流程生产数据,以及各个工序间物料号等信息,按照订单、物料号、时间等查询条件,可追溯到产品在整个制造过程中的过程曲线与过程参数,并进行展示与归档。同时,对各类关系数据提供高级算法(如相关性分析、多元线性回归分析、关联度分析等)进行分析。
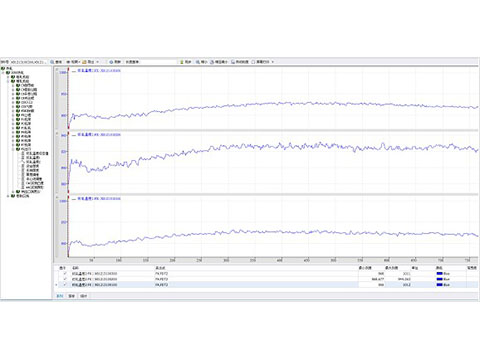
6)质量预测。质量预测的目标是基于机器学习算法,实现多维度、多变量影响下的不能测量类的质量预测。质量预测可以实现模块定制化功能,根据问题特性如性能预报、板形预测、轧机刚度退化预测、夹杂物预测等,选择与之对应的算法进行质量预测。
质量管控系统应用广泛,从单工序到全工序、从板材到棒线材、从钢铁行业到有色行业,采用数据驱动方法为产品质量提升提供了新思路,也得到了企业的高度认可。