一、项目建设背景与思路
中国宝武集团与马钢集团的战略重组,是深化落实长三角一体化国家战略、加强区域经济协同发展的一项务实举措。在携手成为全球钢铁业引领者的道路上,遵照宝武集团“四个一律”要求及智能制造战略规划,马钢致力打造花园式生态文明绿色工厂和智慧制造示范基地。2021年1月4日,中国宝武绿色发展与智慧制造现场会在马钢隆重召开,作为重点展示项目之一,热轧智慧工厂“双线双智控”模式一经推出便引起业内的广泛关注。
经历以自动化、信息化为主要特征的工业3.0阶段后,马钢四钢总厂瞄准行业智能制造前沿,开展热轧智慧工厂“双线双智控”模式的先行示范。双线双智控指项目构建的热轧智控中心覆盖2250和1580两条热轧产线,并包含操维集控平台和协同智慧平台,实现操维和业务双智控。项目以关键绩效指标为牵引,借助精准感知、数字孪生、工艺驱动、智能算法等手段,追求产线极度自动化和业务高效协同化。
作为马钢-北科大产学研合作“基地+”理念的践行者和项目主要建设方,依托“马钢-北科大冶金智能制造技术创新中心”,轧制中心与宝信软件等单位一起携手打造服务于马钢热轧智慧工厂的高质量技术生态圈。在本项目中,轧制中心承担了板坯裂纹检测、精轧跑偏检测与自动调平、新一代密集冷却技术、智能磨辊间、钢卷数据服务、数据可视化、生产任务、质量任务、设备任务、员工成长任务等17个大项。项目组克服建设周期短、任务重及新冠肺炎疫情等不利因素影响,和多方精诚协作,按期高标准完成了项目任务。
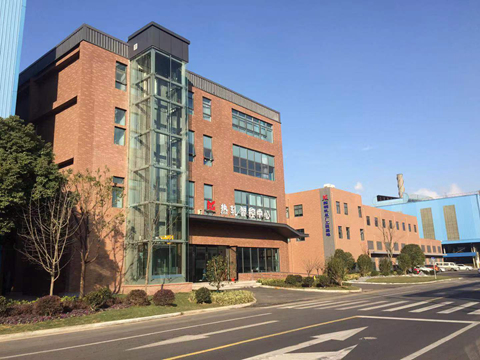
二、操维集控平台
热轧生产过程具有高频、强耦合、非线性等特点,温度、相变、应力相伴相生,远程操维集控的难度远大于其他工序。秉承专业集中管理、工序高效协同的理念,马钢率先开展面向两条热轧线的多区域操维高度集约化探索与实践。
通过新增13项智能装备技术、279个视频传感,连接43个外部系统,实现全域数据感知。在此基础上,通过研发38项关键技术将板坯库、加热炉、轧线、磨辊间、能介、远程运维六大单元进行集中操控,打破区域管理边界,推动生产组织的革新以及员工操作环境的不断改善。
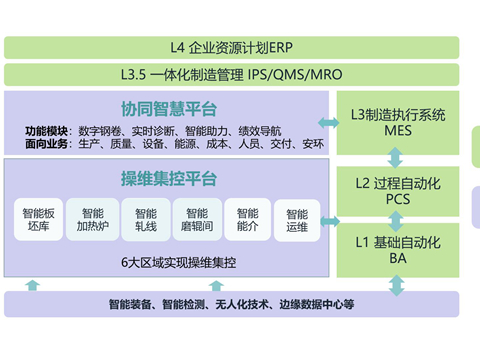
融合促进发展,智慧改变观念,技术变革推动管理变革。操维集控平台建成后,产线之间及岗位之间的协同效应凸显,高效生产模式带来可见效益,马钢四钢轧2250和1580热轧2个分厂整合为1个分厂,12个作业区变为4个作业区,将两线15个岗位整合为“1+2+1” 的新岗位模式(双线板加1个岗位,双线轧钢2个岗位,双线综合运维1个岗位),主线减员超过35%,劳动生产率提升15%。
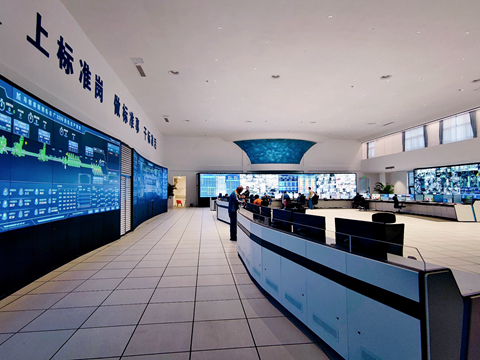
三、协同智慧平台
协同智慧平台依托工业互联网技术集成10万个实时数据点,完成热轧工厂全要素、全区域、全业务数据的集成和融合,构建热轧物理车间的数字孪生体。平台以21个一级指标、420个二级、三级指标为牵引,将热轧车间运行过程生产、质量、设备、能源、成本、交付、人员、安环八大任务进行串接,开发44个智能化模型,形成数字钢卷、实时诊断、智能助力、绩效导航四大主题,并在物理车间和虚拟车间迭代运行,打造生产在线优化和管控精益求精的运行新模式。
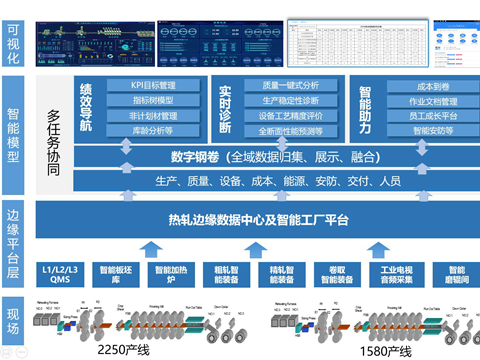
“数字钢卷”聚焦过程参数、产品特性、工序成本、工序能耗等,实现按需分级、数字交付、成本到卷、精益管控。“实时诊断”实现生产故障、质量缺陷、设备精度的实时监控和一键式分析,做到异常过程的快速响应。“智能助力”关注和产线运行密切相关的过程设计、计划上线、实操培训、人员提升,引领知识沉淀和知识更新。“绩效导航”以产品KPI为中心,完成过程指标、产品物流、安环消防的既定目标,引领协同高效运行。
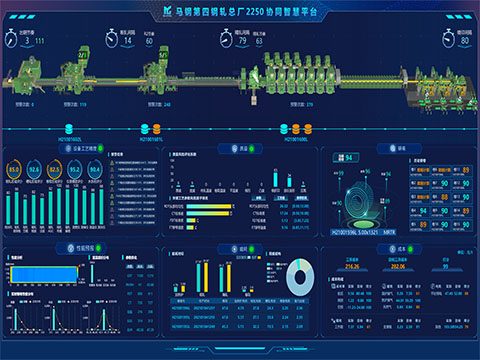
与操维集控平台实现有形工厂改造相比,协同智慧平台聚焦数据感知、知识萃取、优化决策,挖掘热轧海量数据背后的潜在价值,并和操维集控平台相互融合,实现业务间的高度协同和造物育人双管齐下,从全维度提升工厂的智能化水平和软实力,为热轧产能提升15%,成本下降10%,质量提升10%提供强有力保障。
四、项目展望
马钢热轧智慧工厂融入更高效、更精益、更环保、更安全的未来钢铁设计理念,项目构建工厂组织变革的新模式,开创工厂智慧平台的新理念,打造热轧智慧工厂的新样板。
与国内目前冶金各工序常见的生产操作集控相比,本项目在冶金过程大数据应用及应用业务场景完整性方面做出了创新性工作,实现新一代信息技术落地。以大数据为基石的“双线双智控”智慧工厂构架,实现有形工厂改造与无形知识挖掘相得益彰,并形成若干热轧智慧工厂核心技术和钢铁智能制造实践方法体系,走出一条适合马钢的绿色发展、智慧制造之路。