高效轧制国家工程研究中心(以下简称“轧制中心”)为宝钢梅山开发的热轧-冷轧过程质量监控与分析系统近日完成了联合测试,测试效果达到预期。该项目合同于2019年年初签订,依托梅山钢铁1420冷轧产线,开发了热轧-冷轧过程质量监控与分析系统,通过建立多工序数据平台,打通热轧、冷轧工序间的信息壁垒,将热轧工序与冷轧工序的工艺、过程、质量数据集中采集、整合,实现多工序数据共享与追溯。在此基础上,实现过程参数监控、运行状态监控、自动质量判定、工艺过程关联分析、工艺参数优化、模型参数优化、跨工序智能决策等功能,有效提升产品质量与生产过程稳定性。这也是轧制中心全流程质量管控系统(QMS)在国内大中型钢铁企业的第13套应用案例,该项目推进了从基于数据平台的质量通用解决方案到定制化应用的技术升级。随着现代钢铁企业自动化、信息化系统的不断完善,充分利用从数据产生的知识,提升产品质量与生产稳定性成为可能。
目前钢铁企业现有系统亟待解决的问题:1)炼钢、热轧、冷轧各工序、产线之间系统独立,形成数据孤岛;2)工序内部多种维度的过程质量信息分散在不同的系统中;3)基于数据的质量与过程状态异常监控、追溯、分析与优化技术亟待提高。
热轧原料对冷轧最终产品以及生产过程稳定性具有极为重要的影响。由于缺乏热轧工艺质量的准确实时数据信息,现有冷轧生产过程难以就来料状态变化和缺陷问题进行追溯与针对性控制决策,导致焊缝断带、活套跑偏、圆盘剪堵边、轧制力预报精度不高、复杂模态板形缺陷等问题,影响了冷轧工序产品质量与生产稳定性。
本项目基于轧制中心自主开发的全流程质量管控平台,为宝钢梅山1420冷轧提供定制化应用功能:
1)焊缝质量与断带概率预测及优化剪切。根据热轧来料焊缝前后的中点厚度、宽度、断面轮廓、平坦度等状态信息,结合带钢材料特性、焊机实际检测焊缝质量、冷连轧压下率、张力等过程信息与工艺参数,对焊缝质量与断带概率进行预测;同时,在焊接前实施对热轧来料带钢头、尾的剪切量控制,通过建立剪切量优化决策模型,给定剪切值,从而有效降低断带发生概率,并通过精细化控制切损量提高成材率。
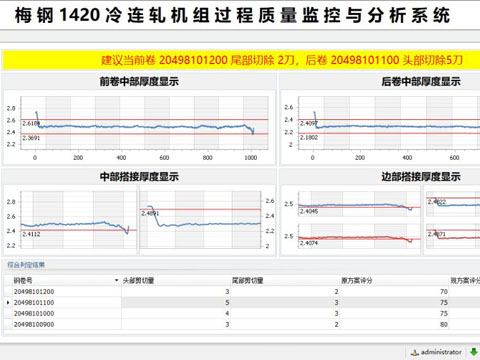
2)冷连轧入口段带钢运行稳定性监控。根据热轧来料的全长中心线偏移、板形、宽度等信息,建立冷轧酸洗活套带钢跑偏预测模型,并结合CPC偏移量检测信息,给出跑偏报警与圆盘剪堵边风险提示,提出合理的运行速度预调整措施,从而充分发挥CPC纠偏辊的纠偏功能,提高纠偏控制效果,降低圆盘剪堵边等事故的发生概率,有效改善冷轧产线的运行稳定性。
轧制中心与宝钢梅山将持续在热轧和冷轧开展基于多工序数据平台的工艺和质量管控应用合作,基于现有主流自动化、信息化系统配置,通过1780、1422热连轧与1420冷连轧产线联动,实现热轧-冷轧-连退一贯制过程质量管控,有效提升产品综合质量与生产运行性能,打造基于工业大数据的智能化工艺控制新模式。